In the world of lean manufacturing and efficient workplace organization, the 5S principles stand out as a powerful methodology aimed at maximizing productivity and minimizing waste. These principles, which include Sort, Set in Order, Shine, Standardize, and Sustain, are designed to create a more organized and efficient workspace. However, one crucial aspect often overlooked is the importance of keeping a process going within this framework. In the context of the 5S principles, _____ means to keep a process going, ensuring that the benefits of these practices are not only achieved but also maintained over time.
Companies striving for operational excellence must embrace the 5S methodology fully, recognizing that the end goal is not just a tidier workspace but a sustainable and efficient process. The principles encourage a culture of continuous improvement and accountability, where every team member plays a part in maintaining standards. Thus, understanding how to keep these processes going is essential for lasting success.
In this article, we will delve into the significance of maintaining the processes established by the 5S principles. We will explore practical strategies for sustaining these improvements and the role they play in fostering an environment of efficiency and productivity. By grasping what it means to keep a process going in the context of the 5S principles, organizations can unlock their full potential.
What Are the 5S Principles?
The 5S principles are a systematic approach originating from Japan, primarily used in manufacturing but applicable across various sectors. The principles are defined as follows:
- Sort: Eliminate unnecessary items from the workplace.
- Set in Order: Organize and arrange tools and materials for easy access.
- Shine: Clean the workspace to maintain a high standard of cleanliness.
- Standardize: Establish standards for processes and practices.
- Sustain: Maintain and review standards to keep processes running smoothly.
Why Is Sustainability Important in the 5S Framework?
Sustainability within the 5S framework is essential for several reasons:
- It ensures that improvements are not temporary but become integral to the workplace culture.
- It fosters a sense of ownership among employees, encouraging them to take pride in their workspace.
- It helps in reducing waste and increasing efficiency over the long term.
How Can Organizations Keep a Process Going?
To ensure that processes remain effective within the 5S methodology, organizations can adopt several strategies:
- Regular Training: Provide ongoing training to employees to reinforce the importance of the 5S principles.
- Leadership Commitment: Leaders should model the behavior they wish to see and actively participate in 5S activities.
- Visual Management: Utilize visual cues and reminders to keep the principles front of mind.
- Feedback Mechanisms: Implement regular check-ins and feedback loops to identify areas for improvement.
What Role Does Employee Engagement Play?
Employee engagement is crucial in the context of the 5S principles. Engaged employees are more likely to:
- Take initiative in maintaining their work areas.
- Report issues promptly and suggest improvements.
- Participate actively in training and development activities.
How to Foster a Culture of Continuous Improvement?
To create a culture of continuous improvement aligned with the 5S principles, organizations should:
- Encourage open communication and collaboration among teams.
- Celebrate small wins to boost morale and motivation.
- Establish a structured approach for implementing feedback into processes.
What Are Common Challenges in Maintaining 5S Practices?
Despite the benefits, organizations may face challenges in sustaining the 5S principles. Common challenges include:
- Resistance to change from employees who are accustomed to old habits.
- Lack of resources or support for ongoing training and development.
- Failure to establish clear accountability for maintaining standards.
In the Context of the 5S Principles, How Do You Measure Success?
Measuring the success of 5S implementation involves both quantitative and qualitative metrics. Some indicators include:
- Reduction in time spent searching for tools and materials.
- Increased production efficiency and output.
- Improved employee satisfaction and engagement levels.
Conclusion: Keeping the 5S Process Alive
In conclusion, understanding what it means to keep a process going in the context of the 5S principles is vital for any organization aiming for operational excellence. By focusing on sustainability, fostering employee engagement, and addressing challenges head-on, businesses can create a thriving environment where the benefits of the 5S principles are not only achieved but maintained. The journey toward continuous improvement is ongoing, and organizations that commit to this path will undoubtedly reap the rewards in productivity, efficiency, and employee satisfaction.
You Might Also Like
Bridging The Gap: Providing Transportation For Rural Workers Living In CitiesExploring The Impact Of Social Media On Heather Brown, Emily Guskin, And Amy Mitchell
From Ice To Earth: The Transformation Of Our Poles
Unlocking Entertainment: The Subscription For $200 For Customers Who Purchase The Streaming Device
Understanding The Choices Of Filmmakers: A Deep Dive
Article Recommendations
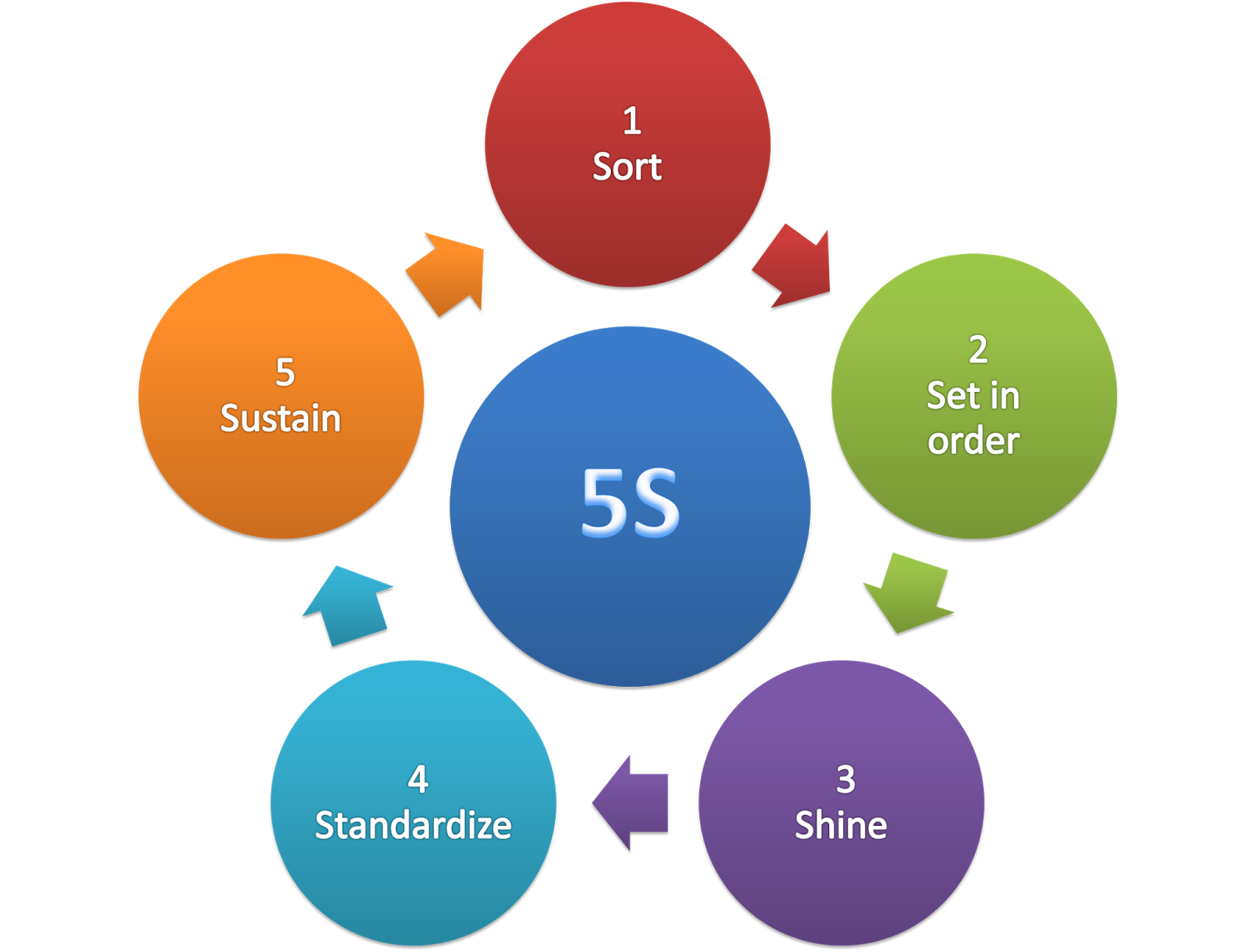
